Overview of the steel industry in Australia
2.1
This chapter gives a broad overview of the steel industry in Australia,
including Australia's primary steel producers and the role of steel
manufacturers and distributors. It also outlines the economic contribution of
the steel industry to the Australian economy and local economies. The chapter
ends with a discussion of the competitiveness of Australian steel and its
contribution to innovation and technology.
2.2
The chapter does not cover in detail international conditions and how
these have impacted the Australian industry – this issue is instead discussed
in chapter 6.
Structure of the steel industry in Australia
2.3
Steel is used in almost all infrastructure and construction.[1]
Significant amounts of steel have been produced in Australia since 1915.[2]Today, the Australian steel industry is an international
leader in coatings, and is recognised globally for its leadership in safety and
product development.[3]
Steel remains an important part of the domestic economy, and the steel industry
employs 90,000–100,000 people around the nation.[4]
2.4
The steel supply chain covers all aspects of steel production, from raw
material inputs, to crude steel and steel products, to manufacturing and end-use
demand for steel products.[5]
The main industries purchasing iron and steel manufacturing products are
manufacturing (48.7 per cent), construction (42.6 per cent) and
mining (5.3 per cent).[6]
2.5
Today, the Australian steel industry consists of various companies
involved in different stages of the steel production and supply chain. The two major
integrated steel producers[7],
BlueScope Steel and Arrium Steel (now Liberty OneSteel), which were both
formerly part of BHP Limited, produce crude steel domestically as 'upstream'
manufacturers, although they produce different products to each other.
2.6
The industry also includes smaller scale operators, manufacturers and
distributors, a network of more than 160 steel distribution and warehouse
premises, 'downstream' supply chains of structural steel fabricators, iron and
steel product importers and recyclers.[8]
BlueScope Steel
2.7
BlueScope Steel is Australia's only producer of flat steel.[9]
Formerly BHP Steel, BlueScope de-merged from BHP Billiton in 2002 to form a
stand-alone public company. The steelworks that it now operates in Port Kembla,
in the Illawarra region of New South Wales, first opened in 1928.[10]
2.8
BlueScope outlined in its submission that its annual steel production
capacity in Australia is 2.6 million tonnes. It manufactures in all mainland
states of Australia and exports approximately 800,000 tonnes a year to various
markets, including the United States, Thailand, Vietnam, the United Arab
Emirates, Malaysia and Singapore. The key focus of the company is:
...higher value, branded products for the building &
construction industry. Products manufactured by Bluescope in Australia include
steel coil and plate, galvanised steels, and a range of coated and painted
steel products... Steel coil and plate products are sold to a range of
manufacturers who convert them into products such as structural steel sections,
girders and beams, fabricated structures, machinery, defence and transport
equipment.[11]
2.9
Following the committee's site visit to the steelworks at Port Kembla, BlueScope's
Chief Executive, Mr Mark Vasella, explained that another key focus of
BlueScope is innovation and research:
Innovation is a key strategy of ours and the basis of our
success in our coated and steel products, which you witnessed today. We are a
small producer of commodity steel by global standards but we are, unusually, a
large manufacturer in terms of value-added painted and coated steel products.
We run an innovation and product development facility here at Port Kembla, with
70 people employed and some 30 PhD qualified scientists. We continue to invest
in our products, such as Colorbond—most recently with the next generation of
Colorbond in partnership with Nippon Steel, our joint venture partner from
Japan. We also invest in the steel innovation hub at the University of
Wollongong.[12]
2.10
BlueScope also supplies products through its Lysaght division which,
according to the division's website, was a pioneering producer of Australian
corrugated iron sheeting used in roofs, sheds and other buildings.[13]
Today, Lysaght rollforms and creates products that include fencing, roof and
wall cladding, rainwater products, steel house framing, structural products
such as flooring systems, walkways and meshes, and home improvement products.[14]
2.11
Between 2011 and 2014, BlueScope reported consecutive net losses after
tax. Mr Vasella stated that 'the current trading environment for BlueScope has
been probably the toughest in living memory'.[15]
2.12
BlueScope outlined in its submission that because of these circumstances,
it had:
...undertaken significant structural transformation, including
halving its commodity steel production in Australia by shutting one of two
blast furnaces, and nominally exiting the export market (although exports
continue due to weaknesses in key domestic markets)... The company has recently
taken action to reduce costs at our Australian steelmaking operations by
approximately $200 million, in order to achieve cashflow breakeven on hot
rolled coil production given current global steel prices and spreads.[16]
2.13
The burden of cost-cutting at BlueScope has fallen heavily on its
workers. In November 2015, BlueScope workers agreed to a new Enterprise
Agreement that triggered 500 job losses, a three‑year pay freeze and the
loss of various employee conditions.[17]
Witnesses from the Australian Workers' Union suggested that because of the
measures employees agreed to so that BlueScope could achieve cashflow
breakeven, some employees experienced financial losses as great as $30,000 a
year.[18]
2.14
The NSW Government announced an assistance package for BlueScope in
October 2015 that involved the deferral of $60 million in payroll tax over
three years.[19]
A federal government assistance package was in turn announced in December 2015,
consisting of $670,000 to assist retrenched workers make the transition to new
jobs, and appoint a local employment facilitator.[20]
2.15
BlueScope reported that it had returned to profitability and payment of
a dividend in the 2015 financial year.[21]
In February 2016, BlueScope announced a $50 million increase in its half‑year
earnings expectations to $230 million, which it attributed to 'earlier [than
expected] delivery of cost reductions, growth in Australia domestic dispatches
and better margins'.[22]
Arrium Mining and Materials
2.16
Arrium, previously known as Onesteel, spun off from BHP in 2000. It was
Australia's only manufacturer of steel long products, and is Australia's
leading steel distributor and reinforcing steel supplier.[23]
The Arrium-owned steelworks in Whyalla, South Australia have operated since
1941.[24]
2.17
Arrium outlined in its submission that its annual steel production
capacity in Australia was 2.6 million tonnes. It produced around 44 per cent of
the total amount of crude steel made in Australia each year, and its share of
the domestic steel production market was approximately 75 per cent.[25]
2.18
Arrium was placed into voluntary administration on 7 April 2016. On 13 July 2017,
Arrium's creditors formally approved the purchase of Arrium's steel division by
international industrial and metals company Liberty House under the banner of the
London-based company GFG Alliance.[26]
Further details of the sale are outlined in Chapter 3.
Steel manufacturers and
distributors
2.19
The Australian steel industry, including both upstream and downstream
supply chains, comprised 12,253 registered businesses as of June 2014. Besides
the major upstream companies, the industry overwhelmingly consists of a large
number of smaller iron smelters, and downstream steel manufacturers and
fabricators, including a network of over 160 steel distribution and warehouse
premises.[27]
The Australian Industry Group reported in its submission that most of these
registered businesses were small: as of June 2014, 93.2 per cent were small
businesses with fewer than 20 employees, and only 6.4 per cent were medium
sized with 21 to 199 employees.[28]
2.20
The Department of Industry, Innovation and Science (Department of
Industry) made a similar observation in its submission, noting that downstream
industries consisted of smaller businesses:
Of the employing businesses, the majority of the firms in the
Iron Smelting and Steel Manufacturing, Iron and Steel Casting, and Steel Pipe
and Tube Manufacturing industries are small businesses employing 1–19
employees. It is only in the upstream industries i.e. the Iron Smelting and Steel
Manufacturing and the Iron and Steel Casting industries where there are any
large firms employing 200 employees or more.[29]
2.21
BlueScope and Arrium also compete in the downstream market, as they both
sell raw steel products to downstream Australian manufacturers and compete
against these manufacturers with their own value-added downstream products.
2.22
Several submitters noted that Arrium and BlueScope's domestic market
shares can be problematic, because they hold a significant degree of market
power and can refuse to supply to or impose particular terms on smaller
industry competitors.[30]
As one submitter observed:
[B]ecause BlueScope and Arrium are so integrated, the smaller
industry participants will generally be required to compete with BlueScope or
Arrium related entities in downstream, value-added markets...
Here-in lies the problem – there are no internal sources of
competition for Arrium or BlueScope. They produce different products from one
another. If an entity cannot purchase steel products from these entities, it
must seek a source from elsewhere, or close-up shop.[31]
Economic contribution of the steel industry to Australia
2.23
The steel industry is an important contributor to the Australian
economy, both in terms of its earnings and as a provider of employment. In its
submission, the Australian Steel Institute referred to ABS data showing that in
2011, the entire steel industry supply chain employed over 100,000 people in
Australia, with an annual turnover in excess of $35 billion.[32]
According to 2013–14 ABS data referred to by the Australian Industry Group, the
upstream steel industry (iron smelting and steel manufacturing) directly employed
about 18,500 people, paid annual wages of $1.5 billion and had an annual
sales and service income of about $11.1 billion.[33]
2.24
A summary of the 2013–14 ABS data provided by the Australian Industry
Group in its submission is shown in Figure 2.1.
Figure 2.1 Australian Steel Industry and Downstream Supply
Chain (2013–14)[34]

2.25
The Illawarra Business Chamber noted that the multiplier effect of the
steel industry in Australia is significant, with 3–5 indirect jobs for every
direct job generated by the industry.[35]
2.26
In its submission, BlueScope stated that it employs approximately 7,500
workers in its Australian operations, thousands more as contractors and
suppliers, and a further 8,500 employees overseas.[36]
Arrium stated in its submission that it employs almost 7,000 people directly, generates
around 14,000 jobs through its activities, and spends nearly $4 billion in
goods, services and taxes annually.[37]
2.27
The Bureau of Steel Manufacturers of Australia in its submission noted
that 'it has been estimated that every dollar of steel production generates an
additional gross output of $2.30 across the wider economy'.[38]
Economic contribution of the steel
industry to local communities
2.28
The Bureau of Steel Manufacturers of Australia also highlighted that 'many
steelmaking facilities are... located in regional centres, and form the basis for
the area's economy'.[39]
The presence of local steel plants leads to flow-on jobs in the education,
health, banking and hospitality sectors, which service steel employees. Two examples
of this are the Illawarra region and Whyalla. Both regional economies are
heavily dependent on BlueScope and Arrium continuing to operate within their
regions.
The Illawarra region
2.29
BlueScope Illawarra on its website reported that it directly employs
around 3,000 people in the Illawarra and indirectly supports about 10,000 jobs
in the region, including contractors, suppliers and other service providers who
depend upon the Port Kembla Steelworks.[40]
2.30
Submitters highlighted that the economic impact of Bluescope's
operations in the Illawarra region is significant. The Illawarra Business
Chamber submitted:
Analysis conducted by Wollongong City Council estimated the
impact of this aspect of BlueScope's business at $1.916 billion per annum
(without taking into effect the multiplier effects). This impact would increase
to approximately $2.572 billion per annum, after taking into account all
direct, indirect and consumption effects.[41]
2.31
Councillor Gordon Bradbery, the Lord Mayor of Wollongong, provided
evidence at the Wollongong hearing that the loss of 500 jobs in the BlueScope
steelworks was anticipated to lead to an economic impact on the local economy
of around $402 million. He also argued that even though the region had
experienced a number of economic downturns because of decreases in the size of
BlueScope's workforce since the 1980s:
Manufacturing remains the most
important sector in the output of the region. It contributes about $7.9 billion
annually in revenue to the region's gross regional product. The manufacturing
sector is the second largest industry in terms of employment, after health and
social services, employing about 8,570-odd people, equating to about 12 per
cent of Wollongong's workforce.[42]
2.32
A representative from the Australian Workers' Union who gave evidence suggested
the closure of the BlueScope steelworks would have a 'devastating effect' on
the region, given the number of jobs and businesses dependent on the steelworks:
We have hundreds and hundreds of people who directly or
indirectly rely on the works. Apart from about a thousand contractors on site,
there are also a number of other contractors, fabricators, who buy product
directly for their work or who do work for the company. [W]hether it be a cafe
shop, the little company that supplies the doormats or the people that take
away the oil and recycle it...[43]
Whyalla
2.33
A range of submitters and witnesses at the Whyalla hearing emphasised
that Whyalla's economy is heavily dependent on the local steel industry.[44]
2.34
In its submission, Arrium outlined the contribution of the steelworks to
Whyalla's economy in more detail:
[The Whyalla steelworks] employs 25 per cent of the town's
workforce and makes up 35 per cent of its economy. The presence of the
Steelworks also provides indirect benefits: other sectors, such as education,
health, hospitality and tourism rely on the population base the Steelworks
provides. This base also ensures access to a level of services from governments
(including schools and healthcare) that generally do not exist in nearby,
lower-population towns.[45]
2.35
The importance of Arrium to the Whyalla economy, and the impact of
Arrium's financial crisis on the city, is further discussed in chapter 3.
Trends in Australian steel production and utilisation
2.36
Integrated steel manufacturing in Australia began in the late nineteenth
century with the discovery of iron ore resources in South Australia. Over the
years, integrated steelworks have closed around the country, with only Arrium
and BlueScope remaining.[46]
2.37
The Bureau of Steel Manufacturers of Australia in its submission
outlined the current largest market sectors for steel:
The two biggest market sectors for steel used in Australia
are steel reinforcement and associated steels used in concrete buildings and
structures, and structural steel and associated steels used in steel framed
buildings and structures.[47]
2.38
Australian steel production mainly uses the Blast Oxygen Furnace (BOF) method.[48]
The weighted capacity utilisation of the BOF in Australia (74 per cent) is
relatively low compared to the weighted world average (81 per cent). Of those
plants that use the Electric Arc Furnace (EAF) method, the capacity utilisation
is very high (97 per cent).[49]
Capacity utilisation 'is calculated as the ratio of actual output to the
reported total (maximum) available productive capacity at each plant'.[50]
These ratios are outlined further in Figure 2.2.
Figure 2.2: Available capacity and capacity utilisation for
crude steel production, by method in 2015[51]
|
Blast Oxygen Furnace (BOF) |
Electric Arc Furnace (EAF) |
Notes |
Available
Capacity (‘000 tonnes) |
Capacity
Utilisation (%) |
Available
Capacity (‘000 tonnes) |
Capacity
Utilisation (%) |
Available capacity includes inactive
or mothballed lines. |
Australia |
6,556 |
74 |
1,558 |
97 |
World (n=677) |
970,816 |
81 |
354,595 |
89 |
Source: MCI Steel
Consultants and Department calculations; capacity utilisation is output divided
by total available plant capacity.
Trends in exporting and importing
2.39
Australian steel output has varied across different decades, from 7.6
million tonnes in 1980, to a peak of 8.9 million tonnes in 1998, to 7.3 million
tonnes in 2010.[52]
In recent years, steel production in Australia has fallen significantly, to a low
of 4.6 million tonnes in 2014,[53]
with a slight increase in production in 2015 to 4.9 million tonnes.[54]
Recent output has been affected by global conditions. The Department of
Industry submitted that:
Australian steel exports have been negatively affected by the
Global Financial Crisis and, until recently, the high exchange rate, with the
export index falling almost two thirds since 2005–06. Imports of steel into
Australia have been less affected, which may be due to some combination of
price effects, the import of varieties not produced in Australia and the
continuing investments in the mining and gas sectors.[55]
2.40
Figures provided by the Department of Industry show that in 2014–15,
Australia exported steel to the value of $692.5 million, and imported $1.7 billion
worth of steel. While the export value of Australia's steel had declined since
2006/07, thanks to the effects of the Global Financial Crisis and, until
recently, a high exchange rate, the import value of steel had also declined,
though to a lesser extent (see Figure 2.3).
Figure 2.3: Indices of Australian steel exports and imports
– 2006‑07 to 2015‑16[56]

Source: Economic and
Analytical Services, Department of Industry, Innovation and Science – Resources
and Energy Statistics
2.41
Further figures in the Department of Industry submission sourced from the
ABS suggest that the raw materials used to create steel are primarily sourced
locally. The figures also show that Australia is a net exporter of flat-rolled
products of iron or non-alloy steel that are not clad, plated or coated. These
products accounted for the largest share of total sales revenue from major
iron/steel products in 2014–15. However, Australia predominantly imports rather
than exports first transformation steel products that are clad, plated/coated
or steel alloys, as well as iron and sheet bars and rods (see Figure 2.4(I) and
(II)).[57]
Figure 2.4(I) and (II): Australian imports and exports of
steel in 2014–15: (I) raw materials and (II) primary steel outputs[58]
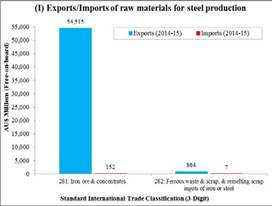

Source: ABS (2016)
International Trade in Goods and Services, Australia. Catalogue No. 5368.0
Figure 2.5: Fabricated imports by calendar year[59]

Source: OneSteel, in Australian Steel Association
2.42
The Australian Steel Industry provided figures showing a dramatic
increase in the number of fabricated imports between 2001 and 2013 (Figure
2.5). As outlined in chapter 6, the global oversupply of steel has led to a significant
increase in imports and this has impacted the Australian steel industry.
Employment
2.43
Arrium commented in their submission that annual industry revenue in the
last five years had fallen by an annualised rate of 7.5 per cent.[60]
2.44
Employment in the steel industry in Australia has been declining steadily
since 2006. Between 2006 and 2011, both full-time and part-time employment in
steel production was above 40,000, but since 2012 has remained below 40,000.
The decline in employment between 2012 and 2015 was around 26 per cent,
compared with 12 per cent in manufacturing for the decade. Figure 2.6
outlines changes in employment in the steel industry between 2006 and 2015.
Figure 2.6: Changes in employment for the steel industry,
manufacturing and all industries between 2006 and 2015 (total employment)[61]
Employment, levels and share |
2006 |
2007 |
2008 |
2009 |
2010 |
2011 |
2012 |
2013 |
2014 |
2015 |
Steel Production
(′000) |
45.5 |
42.3 |
48.8 |
40.9 |
43.1 |
45.4 |
36.2 |
35.7 |
39.7 |
33.8 |
Manufacturing (′000) |
1,009.5 |
1,027.7 |
1,044.8 |
998.2 |
978.7 |
947.3 |
947.8 |
920.1 |
921.7 |
888.6 |
All industries
(′000) |
10,088 |
10,408 |
10,695 |
10,775 |
10,991 |
11,178 |
11,315 |
11,425 |
11,536 |
11,770 |
Steel as a percentage of
manufacturing (%) |
4.5 |
4.1 |
4.7 |
4.1 |
4.4 |
4.8 |
3.8 |
3.9 |
4.3 |
3.8 |
Source: Economic and Analytical
Services, Department of Industry, Innovation and Science; ABS, Labour Force,
Australia, Detailed, Quarterly, Nov 2015, cat.no. 6291.0.55.003
2.45
Despite a global glut in steel supply, and recent falling commodity
prices in the mining sector, demand for domestic steel products remains
considerable. This demand comes primarily from construction services (25.9 per
cent of use as a share of total supply), structural metal product manufacturing
(17.3 per cent), heavy and civil engineering construction (8.2 per cent) and
residential building construction (6.1 per cent).[62]
2.46
The Australian Workers' Union in their submission cited figures
indicating that even though:
...total steel consumption has been fairly stable over the past
seven years, local steel makers have lost a significant share of the total
Australian steel market to imports, falling from a peak of over 62 [per cent]
in 2009/10 to below 56 [per cent] in 2014/15.[63]
Competitiveness of Australian steel production and utilisation
2.47
Factors that make steel competitive include how innovative or
cutting-edge the product is, its value for money and the quality of the finished
product. Factors that influence how cost competitive steel is compared with
steel produced in different contexts include costs involved in production
technology, the regulatory environment, location and demand.[64]
2.48
The Australian Industry Group argued that local steel manufacturers have
several key advantages over international competitors. These include:
-
access to high quality reserves of iron ore and coking coal;
-
the ability to respond quickly to local demand requirements;
-
relatively short lead times;
-
less likelihood of reworks because of misinformation and
mistakes;
-
reduced whole-of-life costs, including maintenance and technical
support;
-
a skilled labour force trained in the latest steel fabrication
techniques and welding processes;
-
strong brand recognition of several product lines; and
-
products that comply with established Australian standards.[65]
Innovation and emerging steel
technologies in Australia
2.49
Several submitters highlighted that one of the
strengths of the Australian steel industry is its track record of producing new
and cutting-edge steel products. These may contribute to the long-term
competitiveness of Australian steel products. The Australian Industry
Group submitted:
The Australian steel industry has a long-standing reputation
for producing high quality products and services backed by a commitment to
investing in technology, innovation and skills development. Modern steel
products are highly sophisticated with new lightweight steel allowing lighter
and more flexible applications that are utilised in the design of cars and
transport equipment, cutting edge medical equipment, defence applications, and
building and construction applications.[66]
2.50
Around 75 per cent of modern steels have been developed in the past 20 years.
This indicates the importance of technology and innovation in the steel
industry, and also the potential for specialisation and niche production.[67]
2.51
Mr Kenneth Watson, the Executive Director of the National Association of
Steel-Framed Housing, gave evidence outlining Australia's position in terms of
steel innovation:
Australia is seen around the world as a leader in the design
and construction of steel-framed buildings using cold-formed steel. The
technological basis for this has been led by BlueScope, with support from many
universities and industry associations around Australia. Due to this leading
technology, Australian companies are exporting products and technology
overseas, particularly to the South-East Asian and African regions. These
technologies include the use of high-strength steels and the development and
application of sophisticated CAD/CAM systems to manufacture steel frames.
[However], recently the overseas countries have been catching up with their
technology and, in some cases, surpassing Australia's leading position.[68]
2.52
The Department of Industry noted in its submission that businesses
classified by the Australian Bureau of Statistics under the Primary Metal
and Metal Product Manufacturing subdivision have a higher level of research
and development (R&D) activity than other industries. For example, between
2008–09 and 2013–14, R&D expenditure as a share of value added for the
primary metal and metal product manufacturing industry ranged from
5.9 to 7.4 per cent; this compared to expenditure between
4.0 to 4.8 per cent for the manufacturing industry and
1.4 to 1.5 per cent expenditure for all industries over the
same period. This was likely because of 'the increasingly technology intensive
production of transformed steel products, as well as the continued improvements
in production technology'.[69]
2.53
Collaboration between iron and steel manufacturing and downstream steel
product manufacturers in Australia has led to the creation of specialised high
strength steel products. These include military products and products for
high-rise construction, storage bins, cement rotating mixers, compactors,
tanker vessels, refinery and petrochemical equipment.[70]
2.54
Other innovations in the Australian steel industry include new
technologies adopted to improve energy efficiency and reduce emissions, and
improvements in plant-heat recovery and air-leakage reduction that have
resulted from technological changes in the sintering stage of the steel
production process. The Australian Industry Group submitted that 'Australia's
leading steel detailing businesses are also at the forefront of international
developments in data interfacing'.[71]
2.55
Liberty OneSteel's recently announced 'green steel' project provides an
example on continuing innovation in the industry. Mr Sanjeev Gupta, Chairman
and CEO of GFG Alliance (owner of the Liberty OneSteel steelworks), announced
in September 2017 that ZEN Energy (also controlled by Mr Gupta) would deliver
renewable energy to power the Whyalla steelworks. The multi-pronged project
will include a mix of solar panels in and around the Whyalla steelworks, and
battery storage and pumped hydro storage in the surrounding region. Mr Gupta
explained:
These first steps in SA will improve reliability and greatly
reduce costs of electricity in our own steelworks at Whyalla, and provide
competitive sources of power for other industrial and commercial users.
This will be followed by early steps to lower Liberty
OneSteel's electricity costs in NSW and Victoria, and to provide power at lower
cost to other industrial enterprises in these states and Queensland.[72]
2.56
BlueScope noted that its operations include innovation and product
development facilities at Port Kembla that employ approximately 70 people,
including around 30 PhD qualified scientists, and at Minchinbury that employ a
further 12 people. It highlighted a new steel coating technology as an
example of an innovative product it had recently developed, which significantly
improved the product's performance and resistance to corrosion, and reduced its
environmental footprint.[73]
2.57
Arrium's Chief Executive of Strategy highlighted:
...the importance of a domestic industry in terms of research
and development, particularly in relationship to new and innovative processes
and technologies...Arrium partners with multiple universities and research
institutions across the country. These partnerships provide us with access to
some of the brightest minds in Australia, and in turn we provide access to
hands-on development.[74]
2.58
Several submitters commented on the work of the Australian Research
Council Research Hub for Australian Steel Manufacturing at the University of
Wollongong, established in 2014.[75]
The Hub's partner is BlueScope Steel, and supporting partners include Arrium,
Bisalloy Steels, the Australian Steel Institute and Lysaght. The University of
Wollongong outlined in its submission the potential benefits of the Steel
Research Hub for the Australian steel industry:
[T]he Australian Research
Council Research Hub for Australian Steel Manufacturing (the hub) is a research
hub bringing together the best and brightest scientists and engineers from
Australia's steel manufacturers and research institutions to drive industry
innovation in product development and improve global competitiveness. The hub
conducts research and development programs that address manufacturing
techniques and best-practice pathways for bringing new ideas to market...
UOW researchers, in a long-standing collaboration with hub
partner BlueScope Steel Ltd, are drawing on expertise in microbiology, surface
engineering, and molecular dynamics to make paints and coatings for steel
sheeting that prevent bacterial growth. Product innovations include a project
to develop a self-cleaning, anti-microbial organic coating for painted sheet
steel to prevent the build-up of mould, algae and other bacteria on roofs,
particularly in humid environments.[76]
Cost-competitiveness
2.59
The Department of Industry in its submission presented figures from 2015
showing how costs in Australian steel plants compare to the rest of the world. On
average, Australian plants using the Blast Oxygen Furnace (BOF) method have a
material cost that is about 10 per cent lower than other plants using the BOF
method in the world in terms of raw materials. However, they also have
significantly higher average labour and overhead costs (54 per cent) and
capital charges (40 per cent). Overall, the cost per tonne output for Australia
on average is about 14 per cent higher than elsewhere in the world.[77]
Input costs are outlined further in Figure 2.7.
Figure
2.7: Contribution of input costs to total product costs – total plant (Blast
Oxygen Furnace), 2015[78]
|
Raw
Materials |
Energy
& Reductants |
Labour
& Overheads |
Capital
Charges |
Total
Cost |
Australian input cost
relative to weighted world average input cost |
-10% |
+6% |
+54% |
+40% |
+14% |
Component share of
Australian total cost |
31% |
25% |
28% |
15% |
100% |
Weighted world average component
share of total cost |
40% |
27% |
21% |
12% |
100% |
Source: MCI Steel
Consultants and Department calculations
2.60
It might be noted that since this data was collected in 2015, energy
costs have increased substantially. Underscoring the challenge for Australian
steel producers in this regard, Bluescope recently reported that its Australian
electricity costs have increased from $59 million in 2015–16, to a
projected $113 million in 2017–18, a 93 per cent increase. Bluescope
further reported that its Australian gas costs have increased an estimated
33 per cent over the same period, from $24 million to
$32 million. Overall, Bluescope's forecast $145 million energy bill
in 2017–18 represents a 75 per cent increase over a two-year period.[79]
Given the large increases in energy costs since the collection of the data
presented in Figure 2.7, it is almost certain the proportionate input cost
attributable to energy will have also increased significantly.
2.61
The Electric Arc Method (EAM) on average is more expensive than the
Blast Oxygen Furnace method, in which crude steel is recovered from recycled
steel. On average, Australian plants using the EAM method have a material cost
that is about 4 per cent lower than other plants using the EAM method in
terms of raw material. Like plants using the BOF method, however, they also
have significantly higher labour and overhead costs than other countries (18
per cent – see Figure 2.8).[80]
Figure 2.8: Contribution of input costs to total product
costs – total plant (Electric Arc Method)[81]
|
Raw
Materials |
Energy
& Reductants |
Labour
& Overheads |
Capital
Charges |
Total Cost per tonne |
Australian input costs
relative to weighted world average cost |
-4% |
-7% |
+18% |
-34% |
-4% |
Weighted input cost share
of Australian total cost |
66% |
13% |
16% |
5% |
100% |
Weighted world average
input cost share of total cost |
65% |
14% |
13% |
8% |
100% |
Source: MCI Steel
Consultants and Department calculations
Factors influencing the recent cost
competitiveness of Australian steel
2.62
The Chief Executive of the Australian Steel Institute gave evidence in
the Canberra hearing outlining some of the factors highlighted by submitters
leading to a current crisis in the Australian steel industry:
The crisis is a global crisis and it is manifest and very
strong in Australia... When you go right through the value chain, all of our
members—fabricators, galvanisers, all of them—are saying that they are
underutilised and suffering profitability strain... What we are sitting in at the
moment is almost a perfect storm for our manufacturers, where the dollar has
stayed stubbornly high, the margins, because of the glut of steel, have shrunk
quite aggressively and the market share is under threat because of the volume
that is available globally. This is a very unique time and it is a perfect
storm... The process is broken.[82]
2.63
BlueScope Steel, in a previous submission to the Productivity
Commission's inquiry into Productivity and the Australian Workplace Relations
System, also commented on recent changes to the global market and how this had
impacted its activities:
At the time of the de-merger [from BHP in 2002], world steel
production stood at around 905 million tonnes. BlueScope manufactured about
5.2 million tonnes of steel per year in Australia. The company's Port
Kembla Steelworks was a low-cost producer, operating in the lowest quartile of
the world steel production cost curve. The average Australian dollar (AUD) – US
dollar (USD) exchange rate was AUD $0.54 cents.
Since then... BlueScope's Australian steel manufacturing
capacity has halved to approximately 2.6 million tonnes per annum, after the
company closed one of two blast furnaces in 2011 as a result of financial
losses, particularly in export markets. The majority of the company's
Australian production is now sold in the domestic market, with approximately
480,000 tonnes (down from 2.6 million) of exports in FY2014 or about 20 per
cent of Australian production and despatches. Import competition has risen
steeply in the domestic market. There has been a significant rationalisation of
businesses in the Australian steel industry.[83]
2.64
The committee also heard from the Bureau of Steel Manufacturers of
Australia that dumping, or the offloading of surplus or subsidised products by
selling them into foreign markets at reduced prices, may create issues for the
cost‑competitiveness of Australian-produced steel.[84]
2.65
Besides global conditions, the Department of Industry in its submission stated
that government policy reforms over the past few decades have also impacted the
domestic steel industry. These include a phased reduction in tariffs on
imported steel, and the implementation of a flexible exchange rate system, both
of which have increased steel manufacturers' exposure to direct competition
from foreign markets. Free Trade Agreements with China, Japan, Korea and
Trans-Pacific Partnership countries, which aimed to increase Australian access
to key markets and reduce import costs for Australian businesses, have further
opened up the market.[85]
2.66
The Chief Executive Officer of the Welding Technology Institute of
Australia gave evidence that, in his opinion, the impact of global conditions
on the Australian steel industry may mean that 'within five years we may not
have a steel industry or a fabricator in Australia'.[86]
These conditions appear to have contributed to Arrium's collapse, as outlined
in chapter 3, and remain a major contributing factor to the uncertainty
surrounding the future of the Australian steel industry.
2.67
International conditions, including the global glut in steel, dumping,
subsidies and other trade measures from foreign governments and their impact on
Australian steel are outlined further in chapter 6.
Energy costs and security
2.68
When this inquiry commenced, energy affordability was not a key focus of
submitters and witnesses. Previously, Australian steel manufacturers had a relative
competitive advantage because of low energy costs compared to the current
environment. However, recent increased energy prices have affected the
viability of energy-intensive manufacturers like steel.[87]
2.69
BlueScope's chief executive noted that escalating energy costs have
contributed to its decline in underlying earnings in 2017. He predicted that
BlueScope's electricity costs will have almost doubled over the two years to
June 2018, and gas costs will have increased by a third during the same period.[88]
This changed situation led the new owner of the Whyalla steelworks, Mr Sanjeev
Gupta, to declare in October 2017 that Australia has the highest energy costs
in the world:
Over the last year, energy prices have doubled and continue
to remain high and, apart from the price increase, the volatility of prices is
intense...It makes Australia the highest-cost energy environment in the world.[89]
2.70
Mr Gupta declared that Australia's high energy costs had led GFG
Alliance to consider ways in which to make the Whyalla steelworks
self-sufficient, and assist in providing solutions nationwide.[90]
This could prevent a situation such as the state-wide power outage that
occurred in South Australia from recurring and impacting the operations of the
Whyalla steelworks.[91]
Committee view
2.71
The committee notes the important role to be played by governments in
defending Australia's steel manufacturing value chain, from steel makers to
steel fabricators, recognising that it is a strategic national asset. The steel
industry supply chain accounts for tens of thousands of jobs nation-wide, with every
dollar of steel production generating an additional gross output of $2.30
across the Australian economy. Further, Australia is a global leader in
innovation and cutting-edge products in particular steel sectors. The committee
considers that securing the future of the steel industry is essential for the
broader Australian economy.
2.72
Steel manufacturers are heavy consumers of energy and extremely
susceptible to price volatility. The evidence provided to this inquiry largely
concerned conditions during the 44th Parliament and did not focus on
energy. However, because of recent price increases in electricity, the
committee is of the view that energy security and affordability is now the
biggest policy issue concern for energy-intensive manufacturers, including steel.
Given the centrality of this issue to the future of the steel industry, the
committee recommends that a bipartisan solution be formulated that will reduce
energy prices and secure supply for steel manufacturers.
Recommendation 1
2.73
The committee recommends that the Australian Government develop a
bipartisan solution to high energy costs that will reduce energy prices and
secure supply for steel manufacturers.
2.74
The most obvious casualty of the recent decline in the revenue and size
of the Australian steel industry is the collapse of Arrium, as discussed in the
following chapter. The committee is concerned that without remedial measures and
a tenable bipartisan plan to reduce energy costs, the future of the Australian
steel industry remains in doubt.
Navigation: Previous Page | Contents | Next Page